What is tinplate?
2023-05-19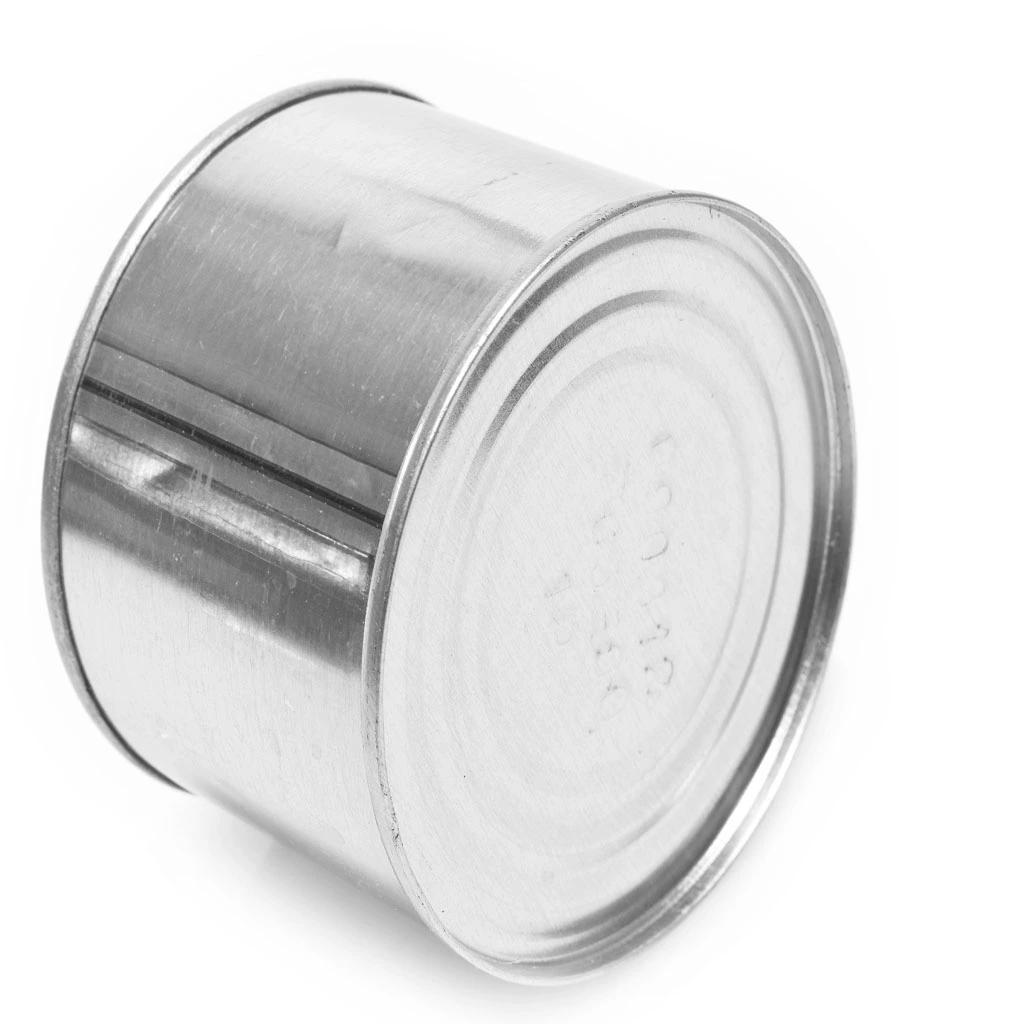
Overview of tinplate
Tinplate is a type of thin steel sheet that is coated with a layer of tin. It is widely used in various industries due to its unique properties and versatility. The process of manufacturing tinplate involves coating a base steel sheet with a thin layer of tin through electrolysis or hot-dipping. This tin coating provides several important benefits to the steel, such as corrosion resistance, increased solderability, and enhanced aesthetic appeal. Tinplate finds extensive applications in the packaging industry, particularly for food and beverage cans, where it serves as a reliable and safe material for storing and preserving a wide range of products. Its excellent barrier properties help protect the contents from external elements, maintain freshness, and extend the shelf life of perishable goods. Tinplate is also utilized in the manufacturing of aerosol containers, metal closures, decorative items, and even certain electrical components. With its remarkable combination of strength, formability, and protective qualities, tinplate continues to be a vital material in numerous industrial sectors.
Manufacturing process of tinplate
The manufacturing process of tinplate involves several steps to create the final product. Here is a general overview of the process:
Preparation of the Base Steel: The first step is to prepare the base steel, which is typically low-carbon steel. The steel is cleaned and treated to remove any impurities, rust, or scale. This ensures a clean surface for the subsequent coating process.
1. Coating: There are two primary methods used for coating the base steel with a layer of tin:
a. Electrolytic Tin Coating: In this method, the base steel sheet is passed through an electrolyte bath that contains dissolved tin salts. An electric current is applied, causing tin ions to be deposited onto the steel surface. The thickness of the tin coating is controlled by adjusting the current density and the duration of the process.
b. Hot-Dipping: Alternatively, the base steel can be coated with tin through a hot-dipping process. The steel sheet is immersed in a molten tin bath at temperatures typically ranging from 450 to 500 degrees Celsius. The tin layer adheres to the steel surface as it is withdrawn from the bath, forming a uniform coating.
2. Surface Treatment: After the tin coating, the tinplate undergoes various surface treatments to improve its appearance and enhance its performance. This may involve applying a chemical passivation layer or oil film to protect against oxidation and improve solderability.
3. Annealing: Annealing is a crucial step in the manufacturing process. The tinplate is heated to a specific temperature and then slowly cooled to relieve internal stresses and improve its formability. Annealing also enhances the adhesion of the tin layer to the base steel.
4. Cutting and Coil Formation: The tinplate is cut into sheets of the desired dimensions or wound into coils for further processing and distribution.
5. Finishing Processes: Depending on the intended application, the tinplate may undergo additional finishing processes, such as lacquering or printing. Lacquering provides an additional protective layer and enhances the visual appeal, while printing allows for branding, labeling, or decorative designs on the surface.
Throughout the manufacturing process, quality control measures are implemented to ensure the tinplate meets the required standards for thickness, tin coating weight, surface quality, and other specifications.
What are the advantages of tinplate?
Tinplate offers several advantages that make it a preferred choice in various industries. Here are some of the key advantages of tinplate:
Corrosion Resistance: Tinplate is highly resistant to corrosion, thanks to the protective tin coating. This makes it ideal for packaging applications, especially for food and beverages, as it helps prevent contamination and preserves the quality and freshness of the contents. Tinplate can withstand exposure to moisture, acids, and other corrosive substances, ensuring long-term product protection.
Solderability: The tin coating on tinplate provides excellent solderability, which means it can be easily joined or soldered to other metal components. This property is crucial in the production of cans and other containers, as it allows for secure and reliable sealing, preventing leakage and maintaining product integrity.
Formability: Tinplate exhibits excellent formability, meaning it can be easily shaped and molded into various intricate forms. It can be processed into different container shapes, such as cans, canisters, and aerosol containers, meeting specific packaging requirements. The flexibility of tinplate enables innovative designs and allows for efficient utilization of space during transportation and storage.
Recyclability: Tinplate is a highly recyclable material, contributing to environmental sustainability. It can be easily and efficiently recycled, reducing the consumption of natural resources and energy required for manufacturing. Recycling tinplate helps minimize waste and supports the circular economy principles.
Safety and Food Compatibility: Tinplate is considered safe for packaging food and beverages. The tin coating provides a protective barrier that prevents any interaction between the packaged product and the metal. It meets stringent regulatory requirements for food contact materials and is widely accepted as a safe packaging material.
Various uses of tinplate in different industries
Tinplate finds extensive use in a range of industries due to its unique properties and versatility. Here are some of the primary applications of tinplate in different sectors:
Packaging Industry: Tinplate is widely employed in the packaging industry, particularly for food and beverage containers. It is commonly used for manufacturing cans, canisters, and tins that hold products such as canned foods, fruits, vegetables, soups, beverages, and infant formulas.
Aerosol Packaging: Tinplate is a preferred material for aerosol containers used in industries such as personal care, household products, automotive, and more. Its ability to withstand pressure, excellent barrier properties, and compatibility with propellants make it suitable for storing and dispensing products in spray form, including deodorants, hair sprays, air fresheners, paints, and lubricants.
Metal Closures: Tinplate is commonly utilized in the production of metal closures for containers such as jars, bottles, and cans. The tin coating enhances the corrosion resistance of the closures, ensuring a tight seal and preventing leakage or contamination.
Electrical and Electronics: Tinplate serves various applications in the electrical and electronics industries. It is utilized in the production of metal casings for electronic devices, electrical enclosures, connectors, and shielding components.
Automotive Industry: Tinplate is employed in the automotive sector for manufacturing components such as fuel tanks, oil filters, and battery casings.
Construction Industry: Tinplate is sometimes used in the construction industry for applications such as roofing and cladding. Its corrosion resistance, durability, and aesthetic appeal make it a suitable choice for certain architectural and decorative elements.
These are just a few examples of the many diverse uses of tinplate in various industries. The material’s properties make it valuable for packaging, protection, decoration, and functional applications across different sectors, contributing to the reliability and performance of the final products.