About Titanium Alloy
2023-05-22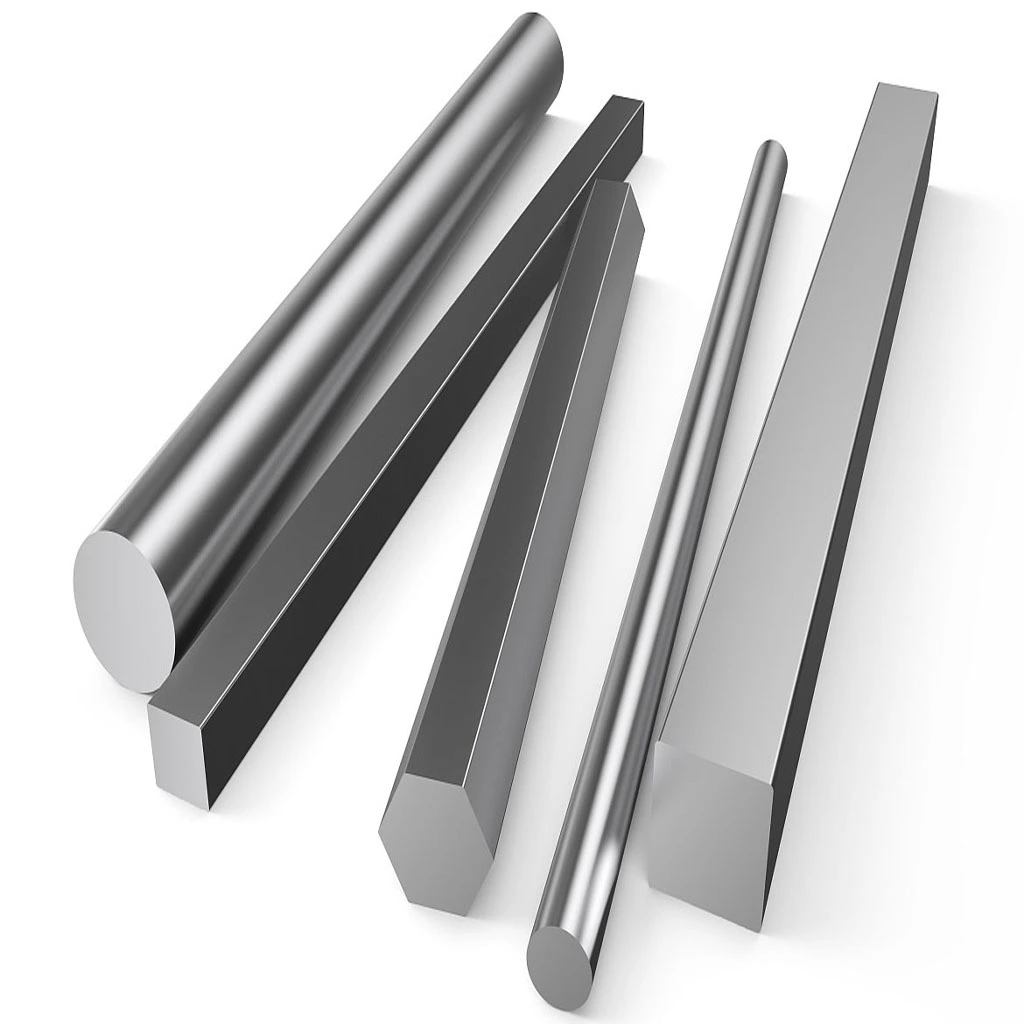
What is titanium alloy?
Titanium alloy refers to a mixture of titanium with one or more other elements to enhance its properties for specific applications. Titanium itself is a strong, lightweight, and corrosion-resistant metal. However, by alloying it with other elements, its mechanical and chemical properties can be further improved.
What are the advantages of titanium alloy?
Titanium alloys offer several advantages that make them highly desirable in a wide range of applications. Here are some of the key advantages of titanium alloys:
High Strength-to-Weight Ratio: Titanium alloys possess excellent strength-to-weight ratios, meaning they provide high strength while being lightweight. This characteristic is particularly beneficial in aerospace, automotive, and other industries where weight reduction is crucial for fuel efficiency, transportation costs, and overall performance.
Corrosion Resistance: Titanium alloys exhibit exceptional corrosion resistance, especially in environments such as seawater and chemical processing plants. They form a protective oxide layer on their surface, which helps prevent corrosion, even in aggressive conditions. This property makes titanium alloys suitable for applications where exposure to corrosive elements is common.
Biocompatibility: Titanium alloys are biocompatible, meaning they are well tolerated by the human body and do not elicit adverse reactions. This makes them highly suitable for medical and dental implants, where the material needs to interact with living tissues without causing harm or rejection.
Excellent Heat Resistance: Titanium alloys can withstand high temperatures, making them suitable for applications that require heat resistance. They maintain their strength and mechanical properties at elevated temperatures, which is important in aerospace, power generation, and other high-temperature environments.
Good Fatigue and Fracture Resistance: Titanium alloys possess good fatigue and fracture resistance, making them durable and reliable in applications subjected to repetitive loading or stress. This property is particularly valuable in aerospace, automotive, and structural engineering, where materials must withstand cyclic loading over extended periods.
Excellent Machinability: Titanium alloys are known for their machinability, allowing for easy shaping, forming, and fabrication into complex components. This characteristic enables efficient manufacturing processes and reduces production costs.
Types of titanium alloys
There are various types of titanium alloys, each with its own specific composition and properties tailored for different applications. Some commonly used titanium alloy groups include alpha alloys, alpha-beta alloys, and beta alloys. Alpha alloys, which primarily consist of alpha phase titanium, offer good weldability and high strength at low to moderate temperatures. They are commonly used in applications such as aircraft engine components and structural parts. Alpha-beta alloys contain a mixture of alpha and beta phases, providing a balance of strength, ductility, and heat resistance. These alloys are widely employed in aerospace, marine, and chemical processing industries. Beta alloys, composed mainly of beta phase titanium, offer excellent high-temperature strength and are often used in applications such as gas turbines, jet engines, and aerospace structures. Additionally, there are specialized titanium alloys, such as Ti-6Al-4V (also known as Grade 5), which are widely used due to their high strength, corrosion resistance, and versatility across multiple industries, including aerospace, medical, and automotive sectors.
Manufacturing process of titanium alloy
The manufacturing process of titanium alloys involves several steps to transform raw titanium and alloying elements into the desired alloy. The process typically starts with the extraction of titanium from its mineral ores, such as ilmenite or rutile, through a series of chemical and metallurgical processes. The extracted titanium is then converted into sponge form, which involves the reduction of titanium tetrachloride with magnesium or sodium. The titanium sponge is further processed through various techniques, such as melting, forging, or powder metallurgy, depending on the desired product form. During the melting and refining stage, the alloying elements are added to the molten titanium to achieve the desired composition. The alloy is then cast into ingots or shaped into billets, which can be further processed through hot or cold working techniques, such as extrusion, rolling, or forging, to achieve the desired shape and mechanical properties. The final steps involve heat treatment processes, such as annealing or aging, to enhance the alloy’s strength, ductility, and other properties. Quality control measures, including non-destructive testing and inspections, are implemented throughout the manufacturing process to ensure the alloy meets the required specifications.
What are the common applications of titanium alloy?
Titanium alloys find numerous applications across various industries. In aerospace, they are utilized in aircraft components, such as airframes, landing gear, and engine parts, due to their high strength, low weight, and excellent corrosion resistance. In the medical field, titanium alloys are widely used for surgical implants, including joint replacements, dental implants, and bone fixation devices, thanks to their biocompatibility and durability. The chemical and petrochemical industries employ titanium alloys in equipment exposed to corrosive environments, such as heat exchangers, valves, and pipes. Additionally, titanium alloys are utilized in marine applications, such as ship hulls and offshore structures, as well as in sporting goods, eyewear, and consumer electronics due to their strength, lightweight nature, and aesthetic appeal.