Heat treatment: Change the properties and structure of metal materials
2023-03-28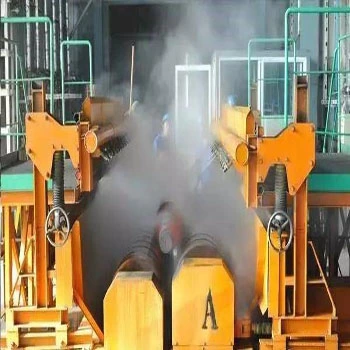
The heat treatment process involves heating and cooling metal materials in order to modify their physical and mechanical properties. By changing the metal’s crystal structure, it is possible to improve hardness, strength, toughness, corrosion resistance, wear resistance and other characteristics. The material must be heated to a required temperature and kept at that temperature for a certain amount of time before cooling in order to facilitate interior structural alterations. There are various methods of heat treatment based on the metal material and application – processes such as quenching, tempering, normalizing, annealing and aging can be used to enhance desirable features.
Basic steps of heat treatment process
The basic steps of the heat treatment process usually include the following stages:
Heating: Heating a metallic material to a temperature that can be above or below the melting point of the material, depending on the desired heat treatment process and the nature of the metal. Heating methods usually include stove heating, induction heating, resistance heating, etc.
Insulation: After reaching the required temperature, the metal material needs to be kept at this temperature for a certain period of time to allow the internal structure of the material to change. The length of holding time depends on factors such as the type, shape and size of the material.
Cooling: After the holding time is over, the metallic material needs to be cooled rapidly to solidify its new structure. The cooling method can be water quenching, oil quenching, air cooling, etc. Different cooling methods can affect the properties and hardness of the material.
What is the heat treatment temperature?
The heat treatment temperature is determined by the required heat treatment process and the properties of the metal material. Different metal materials and heat treatment processes require different temperature ranges.
Taking steel as an example, the commonly used heat treatment temperature ranges from 400°C to 1200°C. The exact temperature depends on the desired heat treatment process and the composition of the steel. For example, quenching requires heating the steel to between 800°C and 1000°C, and tempering requires heating the steel to between 300°C and 700°C after quenching.
Other metal materials also need to determine the most suitable heat treatment temperature according to their properties and required heat treatment process.
What is the purpose of heat treatment?
The main purpose of heat treatment is to change the structure and properties of metallic materials by heating and cooling them, so as to obtain the desired material properties. Different heat treatment processes can produce different effects, such as improving the hardness, strength, toughness, wear resistance, corrosion resistance and so on of the material.
Generally, heat treatment can be divided into two types: tempering and quenching. Tempering is to heat the metal material to a certain temperature and then cool it slowly to reduce the stress inside the material and improve its toughness; while quenching is to heat the metal material to a high temperature and then cool it rapidly to increase the hardness and strength of the material.
In addition to tempering and quenching, there are other heat treatment processes, such as annealing, normalizing, surface hardening and so on. Each heat treatment process has its unique advantages and scope of application, and the appropriate heat treatment process can be selected according to specific application requirements.
Types of heat treatment process
Heat treatment processes can be divided into many types, each with its own unique scope of application and purpose. The following are several common heat treatment processes:
Tempering: Heating the quenched metal material to a certain temperature and then cooling it slowly to reduce the stress inside the material and improve its toughness.
Quenching: Heating a metal material to a high temperature and then cooling it rapidly to increase the hardness and strength of the material.
Annealing: Heating a metal material to a certain temperature and then cooling it slowly to improve its internal structure and increase its toughness.
Normalizing: Heating a metal material to a certain temperature and then cooling it to room temperature in order to improve the structure of the material and increase its strength.
Quenching and tempering (Quench and Tempering): Quenching the metal material first and then tempering it to improve its hardness and strength while maintaining its good toughness.
Surface Hardening: Form a hardened layer on the surface of metal materials to improve its surface hardness and wear resistance. Common surface hardening methods include gas carburizing, ion carburizing, and nitriding.
Four basic processes of heat treatment
1.Quenching: The quenching of steel is to heat the steel to a temperature above the critical temperature Ac3 (hypoeutectoid steel) or Ac1 (hypereutectoid steel), keep it warm for a period of time to make it austenitized in whole or in part, and then austenitize it with a temperature greater than the critical temperature. A heat treatment process in which the cooling rate is quickly cooled to below Ms (or isothermal near Ms) for martensite (or bainite) transformation.
Application range: quenching process is the most widely used, such as tools, measuring tools, molds, bearings, springs and automobiles, tractors, diesel engines, cutting machine tools, pneumatic tools, drilling machinery, agricultural machinery, petroleum machinery, chemical machinery, textile machinery, aircraft, etc. Parts are using quenching process.
2.Tempering process
Tempering is a heat treatment process that reheats the quenched workpiece to an appropriate temperature lower than the lower critical temperature, and then cools it to room temperature in air, water, oil and other media after holding it for a period of time.
The purpose of tempering: (1) Eliminate the residual stress generated when the workpiece is quenched to prevent deformation and cracking; (2) Adjust the hardness, strength, plasticity and toughness of the workpiece to meet the performance requirements; (3) Stabilize the structure and size to ensure Accuracy; (4) Improve and enhance processing performance.
3.Normalizing process
Normalizing is a metal heat treatment process in which the steel is heated to 30-50°C above the critical temperature (full austenitization temperature), and after holding for a proper time, it is taken out of the furnace and cooled in the air or sprayed with water, sprayed or blown.
Purpose: (1) to refine grains and homogenize carbide distribution; (2) to remove internal stress of the material; (3) to increase the hardness of the material.
4.Annealing process
The material is heated to a specific temperature and held for a period of time, and then cooled slowly to soften the material, reduce internal stress, and improve cutting performance. The essence of annealing is to heat the steel to austenitize and undergo pearlite transformation, and the structure after annealing is close to the equilibrium structure.
Purpose of annealing:
(1) Reduce the hardness of steel, improve plasticity, and facilitate machining and cold deformation processing;
(2) Homogenize the chemical composition and structure of the steel, refine the grain, improve the performance of the steel or prepare the structure for quenching;
(3) Eliminate internal stress and work hardening to prevent deformation and cracking.