What is Martensitic Steel (MS)?
2023-05-24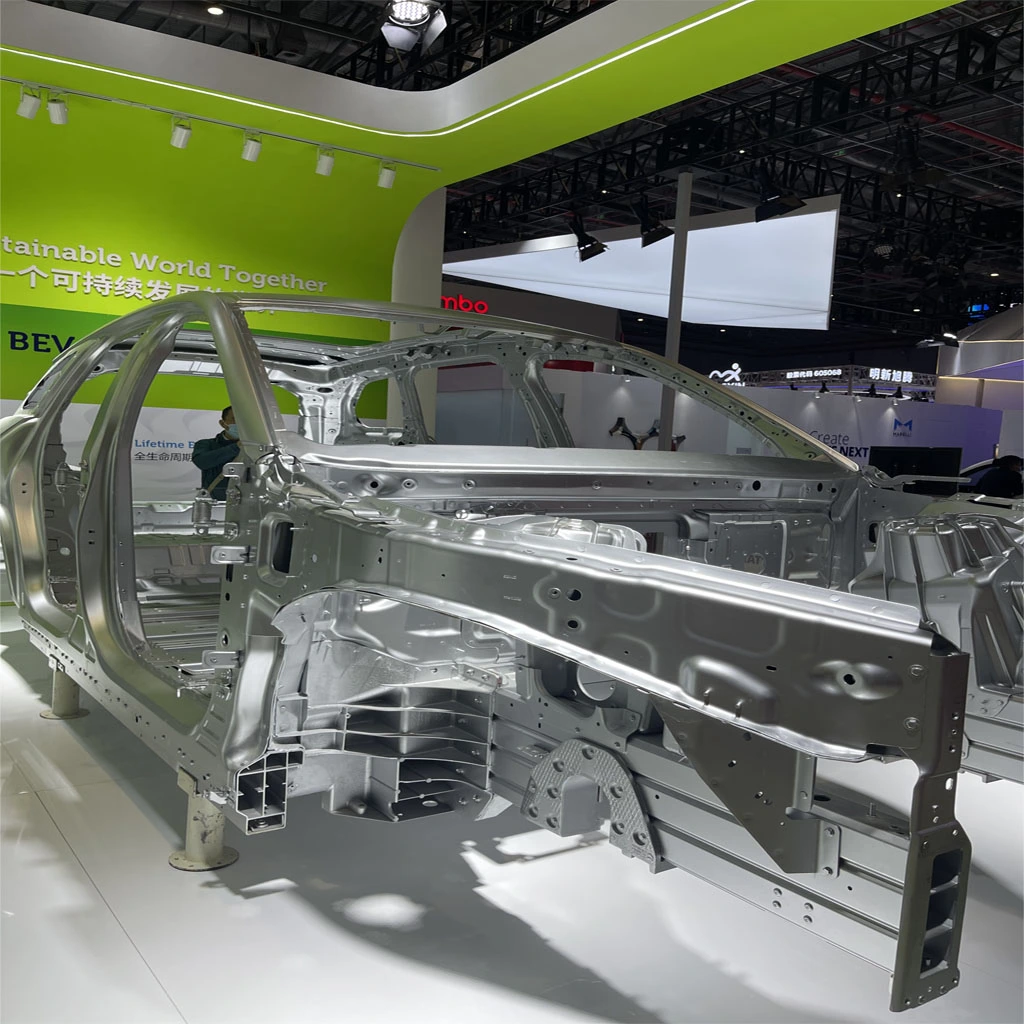
What is Martensitic Steel (MS)?
Martensitic steel (MS) is a type of steel alloy known for its exceptional hardness, strength, and wear resistance. It derives its name from its characteristic microstructure, which consists predominantly of martensite—a hard, crystalline phase that forms during rapid cooling or quenching from high temperatures. Martensitic steel is primarily composed of iron, carbon, and other alloying elements such as chromium, molybdenum, and nickel, which contribute to its unique properties. The high carbon content in MS enables the formation of martensite, resulting in a material with superior hardness and tensile strength. This makes martensitic steel particularly well-suited for applications requiring excellent cutting, abrasive, and impact resistance, such as knives, cutting tools, bearings, turbine blades, and certain structural components. Additionally, martensitic steel exhibits good corrosion resistance, making it suitable for various environments, although not as resistant as stainless steels. Its remarkable combination of hardness, strength, and corrosion resistance has established martensitic steel as a widely used material in industries ranging from automotive and aerospace to oil and gas.
What are the advantages of Martensitic Steel?
Martensitic steel (MS) offers several advantages that make it a desirable material for various applications:
High Hardness: Martensitic steel possesses exceptional hardness due to its microstructure consisting primarily of martensite. This hardness enables it to withstand heavy loads, resist deformation, and maintain its shape under demanding conditions.
Strength: Martensitic steel exhibits high tensile strength, making it capable of withstanding significant stresses and forces. This strength is crucial in applications where structural integrity and durability are paramount.
Wear Resistance: The hardness of martensitic steel imparts excellent wear resistance, allowing it to withstand abrasive conditions and resist surface damage. This makes it well-suited for tools and components subjected to friction, cutting, or sliding wear.
Corrosion Resistance: Although not as corrosion-resistant as stainless steels, certain grades of martensitic steel can exhibit good resistance to corrosion, particularly in comparison to other steel types. This makes it suitable for applications in environments where corrosion may be a concern.
Ease of Heat Treatment: Martensitic steel is known for its ease of heat treatment, enabling manufacturers to achieve desired mechanical properties through processes such as quenching and tempering. This flexibility in heat treatment allows for tailoring the material’s characteristics to specific applications.
The Process of Martensitic Steel
The production of martensitic steel involves a series of carefully controlled processes to achieve its unique microstructure and desirable properties. The starting point is typically a composition of iron and carbon, along with other alloying elements such as chromium, molybdenum, and nickel. The carbon content is crucial as it determines the ability of the steel to transform into martensite during cooling. The manufacturing process often begins with melting and refining the raw materials in a furnace, followed by casting the molten steel into desired shapes or ingots. After solidification, the steel undergoes hot working processes like rolling or forging to shape it further.
The critical step in producing martensitic steel is the heat treatment known as quenching. The steel is heated to a high temperature, typically above the critical transformation temperature, to dissolve any carbides and austenite present. It is then rapidly cooled by quenching in a medium such as oil, water, or air. This rapid cooling prevents the formation of other microstructures, such as pearlite or bainite, and promotes the formation of martensite, a hard and brittle phase.
Following quenching, the steel may be subjected to a tempering process to enhance its toughness and relieve internal stresses. Tempering involves reheating the steel to a specific temperature below the critical transformation temperature and holding it for a certain duration, followed by controlled cooling. This step imparts desired mechanical properties by adjusting the martensitic structure, balancing hardness with improved ductility and toughness.
The precise parameters of heat treatment, including heating temperatures, cooling rates, and tempering conditions, are carefully controlled to achieve the desired microstructure and properties of martensitic steel. This process allows for customization and optimization of the steel’s characteristics, making it suitable for a wide range of applications requiring high hardness, strength, and wear resistance.
What auto parts are Martensitic Steel typically used for?
Martensitic steel (MS) finds application in various automotive components that require high strength, hardness, and wear resistance. Some typical auto parts where martensitic steel is utilized include:
Engine Valves: Martensitic steel is commonly employed in the manufacturing of engine valves due to its excellent wear resistance, high temperature strength, and resistance to valve seat recession. These properties allow the valves to endure the harsh conditions within the engine, such as high temperatures, combustion forces, and repetitive impacts.
Camshafts: Camshafts, responsible for operating the valves in an engine, often incorporate martensitic steel due to its combination of strength, hardness, and wear resistance. The cam lobes that come in contact with the valve lifters and push rods require a durable surface, making martensitic steel an ideal choice.
Piston Rings: Martensitic steel is used for piston rings to withstand the high pressures and temperatures encountered during engine operation. The rings require hardness and wear resistance to maintain a tight seal between the piston and cylinder walls, preventing gas leakage and ensuring efficient combustion.
Transmission Gears: Martensitic steel is well-suited for manufacturing transmission gears, especially in applications involving high torque and heavy loads. The hardness and strength of martensitic steel enable the gears to endure the demands of power transmission while resisting wear and deformation.
Suspension Components: Some suspension components, such as stabilizer bars or sway bars, may utilize martensitic steel due to its ability to withstand bending and torsional forces without undergoing plastic deformation. The high strength and toughness of martensitic steel make it suitable for these critical load-bearing components.
Steering Components: Certain steering system components, such as steering shafts or pitman arms, may incorporate martensitic steel. These parts require high strength and resistance to fatigue and wear to ensure precise and reliable steering performance.
Fasteners: Martensitic steel is often used for automotive fasteners, including bolts, studs, and screws. These fasteners require high strength, hardness, and resistance to shearing forces to securely hold components together in various automotive assemblies.
The specific selection of martensitic steel in these auto parts depends on the desired mechanical properties, operating conditions, and design considerations for each component. By incorporating martensitic steel in these applications, manufacturers can enhance the performance, durability, and reliability of automotive systems.